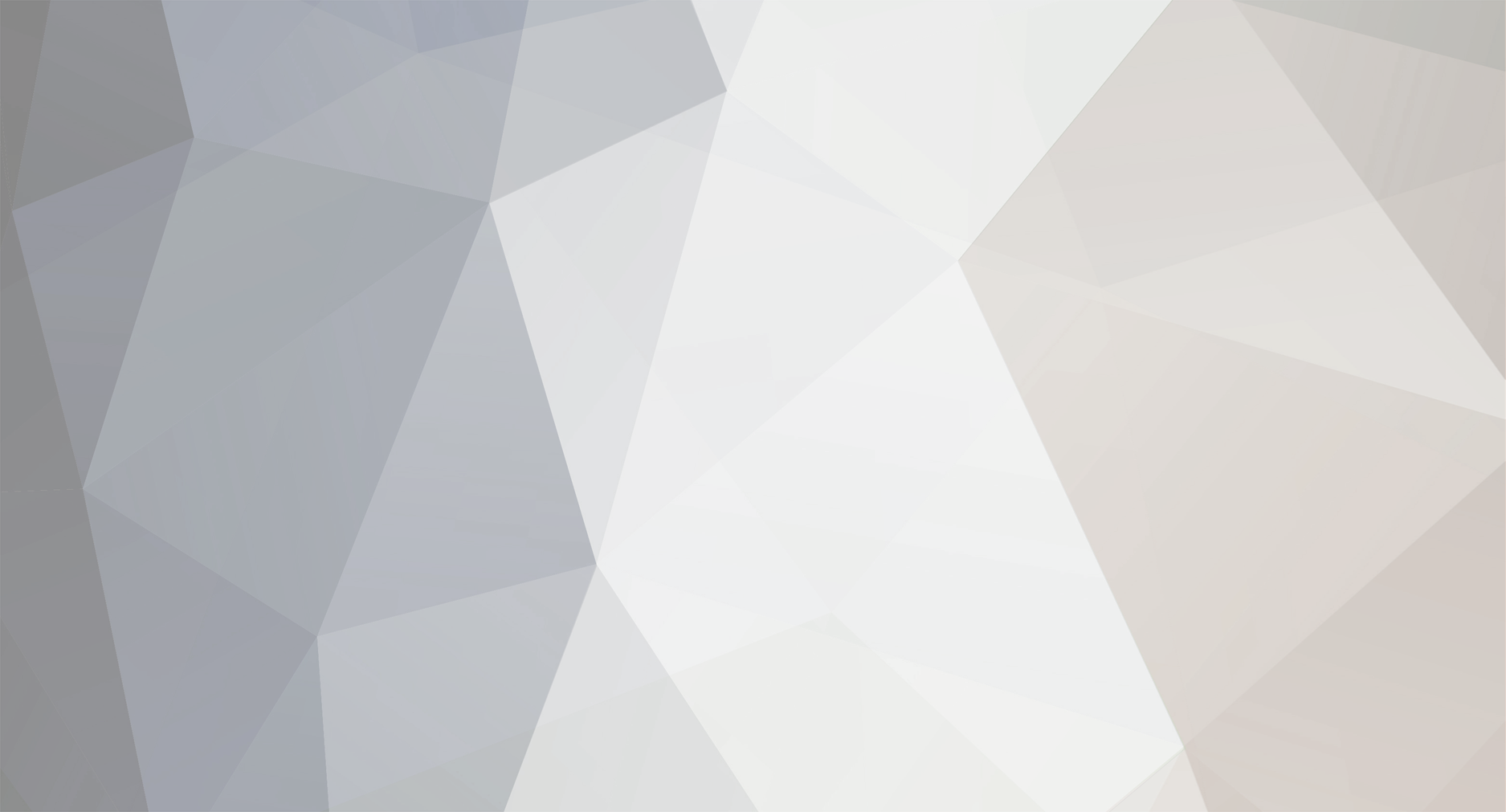
Mario
Free Member-
Posts
169 -
Joined
-
Last visited
-
Days Won
6
Content Type
Forums
AutoShopOwner Articles
Downloads
Blogs
Gallery
Profiles
Events
Store
Links Directory
Shop Labor Rates
Community Map
Everything posted by Mario
-
I have disabled vehicles that are not paid for when dealing with fishy customers. Most customers won't figure something simple as pulling coil power, fuel pump fuse, etc... I also have two steering wheel locks I use. I try to remove them before we open so if a customer sees them they don't get the wrong impression, but its hard to trust anybody.
-
I Haven't had a car hit by an employee/customer during business hours, but I had a drunk spash into a Minivan at night that was in the lot. I just paid out of pocket, it was only a couple of hundred over my deductible and I did not want to report it to the insurance.
-
I shop for the best price on parts that I can, but I can't help myself but sit back and chuckle a little. We want our customers to pay top dollar for quality service and professionalism, yet on our side of the counter we whine and complain over finding the cheapest or near cheapest priced parts we can get ahold of. I feel like the price shopping customer we all get annoyed by. I generally buy from a local wholesaler called car parts warehouse. I do shop with az and advance due to proximity and wide selection of in stock odd ball parts. Tires come from American tire distributor
-
When to replace Transmission fluid and other fluids?
Mario replied to Joe Marconi's topic in Repair & Maintenance Services
I don't change transmission fluid on higher mileage vehicles or ones with dark fluid. I have been burned before. Transmission Fluid 30-40k drain & fill. Brake Fluid 40k Coolant 60k. I say modern engine oils and filters at 5k, but so many cars still consume/leak oil that by 5k it can become very low. 3k for that reason alone. ---------------------------------------------------------------------------------------------------------------------------------------- Everything anymore seems like it is advertised as "lifetime" or 100k. Technically it is lifetime. They pour it in at the factory, and you don't change your transmission fluid for the life of the transmission until it dies ealry :-) -
Tough Dealings with Extended Warranty Companies
Mario replied to Joe Marconi's topic in Workflow, Procedures, Shop Forms
The worst is Cars out of Pennsylvania by far. $60/hr Cap based on labor guide and they search online for the cheapest part and that is what they will pay for the part. They have no concern if the vehicle is disassembled on your lift and you have to wait 2-3 days for their online part. They charge the customer a $100 deductible and customer pays for diag and anything over their limit. -
I always tell the customer before we do the repair the possible outcome of it needing more work then we can tell from a diagnostic without actually opening up the part at question for visual inspection (more $$$). Example today we had a F150 4x4 with ABS Brakes that were kicking on early. Scanned it, no codes. Viewed the live data, the LF was dropping off at the end of the stopping process (2-3 mph before the truck came to a standstill) and the ABS would kick on. Told the customer it needs a LF Wheel Bearing Assembly (sensor and ring included). It could be both hub units if the other is worn as well. Did the LF, fixed the problem, but he was prepared to pay double if it needed the RF as well. I would go back and see why the vehicle is idling rough. Vacuum leak? Misfiring? It needs more diagnostic. Whatever it needs to fix it, it needs to fix it. Its not your truck, I wouldn't put any of your money/shops money into making it run for the customer. You diagnosed a non-running vehicle, it runs now, but needs a little more work. If this scenario is what I am invisioning it to be, the customer is now trying to pass the burden to make it 100% onto you? Its happened here before, many try it, nobody has any shame lol. It why when things come in non-running and its internal damage, I really try to sell a used/reman engine or trans with a parts & labor warranty from the supplier just to avoid the headache.
-
Need a tire balancer and changer
Mario replied to Pjauto's topic in Automotive Shop Tools & Equipment
What is your objective with the tire machine, what are you trying to do? Do you want to be a full fledged tire shop? I don't know how similar our situations are, but I am right across the street from a used/new tire shop that has 3 or 4 tire machines in it, and all they do are tires, and they get a very substantial discount on used and new. I wanted a tire machine and wheel balancer just because I was tired of paying them $15 to mount & balance tires for me. I also wanted the balancer to help diagnose/solve driving issues. I picked up a used Accu-turn 5500 from a shop that upgraded for $450. Its a pretty nice balancer and does up to 20" wheels. I was changing tires for about 6 months with a manual machine. It wasn't as bad as it sounds. Another shop upgraded to a new tire machine and had a Coats 20/20 for $100. I've been using that since. It only does up to 17" wheels and nothing low profile, but it works for 95% of the cars we work on which are normally 6year old to 20 year old cars that don't have the 18" alloys on them. I'm always looking to upgrade from the Coats when something is available. I can say my $550 investment has paid off pretty quickly which is tough to say in this business! -
Very competitive in my area with a tire shop being basically on every major corner. I have had okay results with just marking up $100 on four tires, or $50 on two. That includes mounting, balancing, and I add a $2 fee for tire disposal if they leave the tires with me. Some shops still install all four for what I can buy all four tires for at cost. I have no idea how. I have an old machine and I don't mount tires fast enough to really make money over my hourly rate. I spend too much time with the wire wheel cleaning the wheels but I hate having to redo them over bead leaks. Good luck!
-
While on the subject of easy to work with lines, and rust resistant lines, another excellent product that is easy for technicians to work with and will not rust again are the SUR&R nylon/plastic Fuel Line kit. It gives you all the common fuel line fittings (but improved design, easy to disconnect, no more disconnect tools) and the appropriate size line and compression fittings to do nylon patches on steel lines (if only a section is rusted out), or to run complete lines from the tank to the engine. It saves a lot of time from having to source OE replacement lines, is safer and more professional then high pressure rubber with high pressure fuel clamps, and it will not degrade like rubber over the years, and it will never rust! I will never run metal fuel lines again, and all of my patches are done with this stuff.
-
The Copper Nickle Alloy line has been out for some time now, and it is all I will use at the shop, I don't even stock steel line. - It does not rust - It is difficult to kink - It is easy to bend - It is easier to cut & flare It is the one product where there are no negatives, not to mention it is only $4 more a roll through my supplier then traditional steel line. I have never heard of these lines absorbing brake fluid and I have never had one customer complain about break fluid loss. Copper may absorb brake fluid (?) but this is Copper Nickle Alloy, not a standard copper line.
-
Buying a fully equipped shop..Worth this money?
Mario replied to sparkerauto's topic in General Automotive Discussion
I'd be caution of taking over any shop with $10k of expenses right off the bat. -
Low working wages in the area, still crawling out of an economic recession, and a competitive auto repair market here. We charge 30% mark up on MOST parts. You mark up large parts here ($200+) it will throw your estimate to high and say bye bye to the repair job. Every customer seems to be a price shopper and they know the fair market price before they call or enter the door. I don't lose out on too many jobs with this method ($60/hr labor + reasonable 30% mark up). It would help to charge more, but it is either win the bid, or sit on the computer all day.
-
AutozonePro offers ESTIMATING software from ALLDATA with Invoicing for $50/month. There are also alternatives such as RealTime Labor Guide for $300 and it is your forever unless you update. The estimating software is what is valuable to me, the repair information can all be found on google and normally is quite useless anyways.
-
Just about all the lifts are made in China anymore, very few USA manufactured lifts. I have not used the Atlas brand lifts, but I do know Gregg Smith Equip. does have a solid reputation with those who have used the lifts. The company that sold me my lifts sells off brand, BendPak, Danamar, Quality, Challenger etc... The installer told me EVERY shop (including dealerships) are going to the off brand lifts because there is not a big drop off in quality and they simply are a much better price. I have a China built drive on and 2 post with no problems. I wouldn't hesitate to buy them again. My biggest concern at the moment is the concrete under the 2 post lift, but nothing to do with the lift itself.
-
I have tried several different brands. For a while I was using Bendix Globals. The pad itself is okay, the issue I had were the shims on the outside of the pad coming loose. They are only held on by some bent over tabs, and once the tabs are bent any which direction even the smallest bit, they squeal. Right now i use the Duralast Gold from Autozone. They are a little more expensive, but the shims are held in place by rivets and cannot be removed. So far I have had 0 complaints from customers and I have installed them on dozens of cars.
-
Yes they did and so did every politician before them. We spend too much money and we spend it on the wrong things. Our government is a carbon copy of the american house holds in general. As Americans we buy with debt and just pay monthly balances until we die. We do it on everything; houses, cars, businesses, dinner. If we act like that, what do we expect our elected officials to do?
-
how do i compete with mobile/backyard mechanics?
Mario replied to carbtech72's topic in Dealing With Competition
A northstar engine out of a deville is not a cake walk swap. I'll bet dollars to donuts that the customer will end up with a half taken apart car that never gets put back together for $900. In all varies by area, but around here about $1300 in labor is probably average for that replacement plus engine cost and any lines/hoses that need replaced during the removal and reinstallation. -
My shop is in a working class neighborhood where used tires are in demand for a lot of individuals and families. Even the higher income individuals are still seeking deals for tires on seasonal wheels. Used tire shops are not a rarity around here, but most are run out of small buildings with tire removal done in the parking lot. I bought the tire machine to do new tires on, but I was scoping out other shops a few days ago, and the new tire/light service shops are empty (Monroe, Midas, other independent light service shops), and the few shops doing used tires are packed. I know the used tire shops do not pay more than $5 a tire from the supplier, and sell them installed for $35-$45 for most cars, with larger truck tires obviously being more. I know new tires are a better value, but the market in the area demands what the market in the area demands. I've been swamped all week so I have not had time to even think of searching for suppliers until I put up this post, but I am going to do some research on it hopefully in the middle of next week. The kicker is, when I did speak to one NEW tire supplier, there is more room left for profit in a used tire install then on most new tire installs (based on local rates).
-
how do i compete with mobile/backyard mechanics?
Mario replied to carbtech72's topic in Dealing With Competition
I don't compete with them. I have a professional shop with service bays, specialty equipment, resources, insurance, and a warranty. They don't. I have heard of tons of bad repairs with backyard/mobile mechanics. What is the customer going to do when their new engine doesn't run properly, is the backyard mechanic going to be back? What is the customer going to do when the backyard mechanic abandons the job half done in their driveway? -
I recently picked up a tire machine and I am getting a balancer as well. In my area, we have a market of customers looking for used tires, I get asked weekly. I currently don't do ANY tires, but I am strongly considering stocking common sized used tires for older vehicles as these seem to be the customers generally asking for them. I believe it would also be a great opportunity to do brake & front end inspections while the tires are off the vehicle and upsell needed repairs. Do any owners sell used tires and what are your sources for obtaining them (recyclers, resellers).
-
I only have one mechanic so it may be different, but I own the special tools and don't expect him to buy them. I have the Digital Multimeters, the Scantools, the ball joint presses, the special sockets, the torches, welders, air hammers, diagnostic equipment. I only expect my mechanic to have basic hand tools needed to complete most jobs, ie: sockets, wrenches, ratchets, breaker bars, screw drivers etc... If a specialty item is needed it comes out of the shop account and I try my best to decide whether we can take on this job or not (depending on whether or not we expect to do more of these repairs).
-
This is why I like AutoZone for most of our parts. Although I haven't had many issues with parts, when I do, they replace the part and credit our account for the labor with very little hassle. Items like alternators, starters, struts, shocks etc... are 100% labor reimbursement. We also use Car Parts Warehouse. They have good prices, but all warranty claims are through the manufacture which can be a pain.
-
Decreasing prices to make more sales?
Mario replied to Joe Marconi's topic in Accounting, Profitability, & Payroll
I noticed some shops here get customers in with a low ball over the phone quote, then the price climbs up during the repair. I rarely ever have an issue selling a fair priced repair to a customer in person, what I don't have any luck with is selling over the phone. Seems people just call every shop and take the lowest price. Unfortunately I am not always the lowest price, never the highest price, but a fair price (although I am one of the LOWER prices). -
Yes, it was CARS.