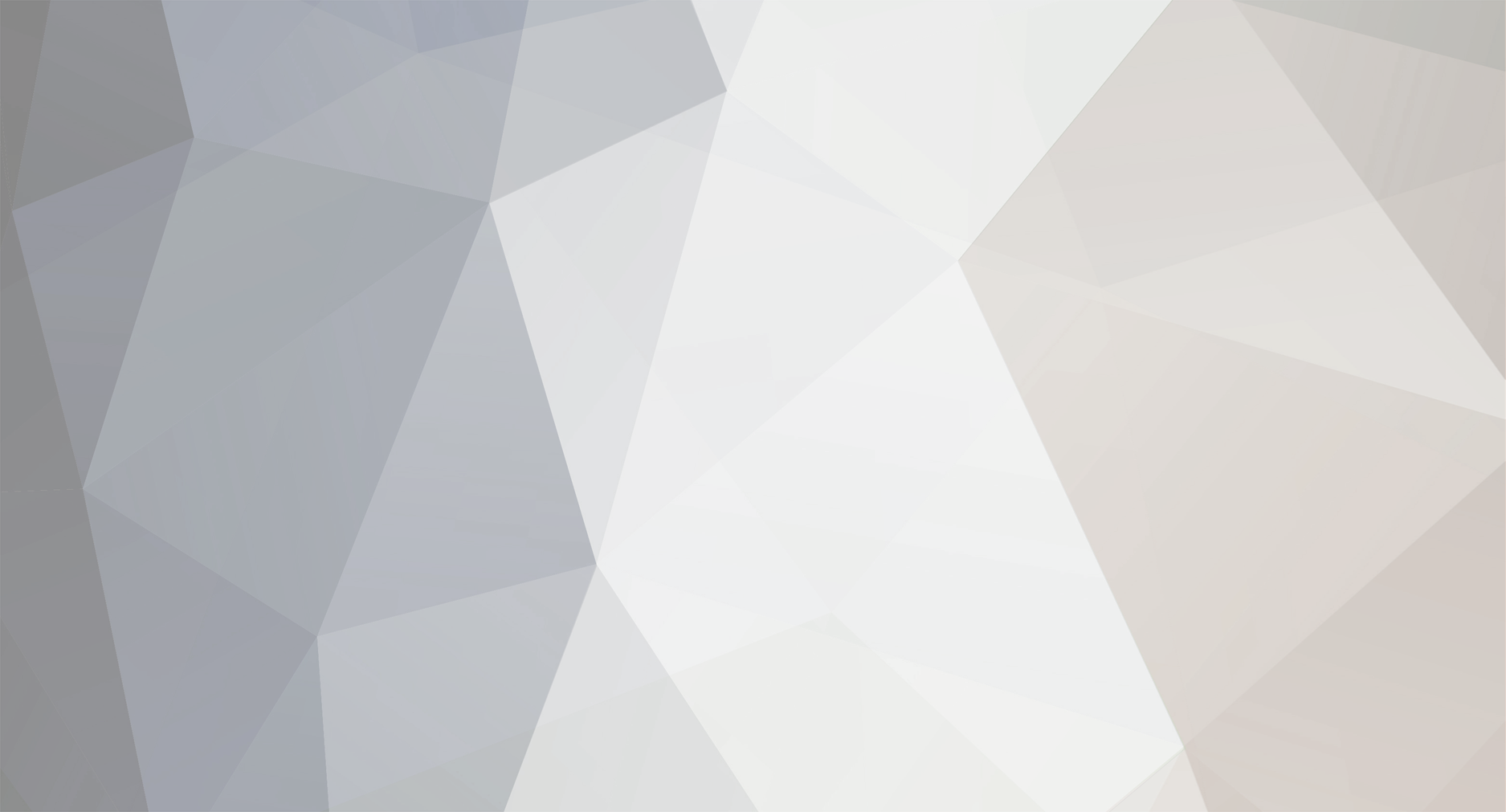
JimO
Free Member-
Posts
143 -
Joined
-
Last visited
-
Days Won
18
Content Type
Forums
AutoShopOwner Articles
Downloads
Blogs
Gallery
Profiles
Events
Store
Links Directory
Shop Labor Rates
Community Map
Everything posted by JimO
-
I presently have one bulk oil tank that is dispensed from an overhead reel in the shop and we use case goods for all other needs. The bulk oil route was great years ago but late model vehicles require so many different oils that most of my volume is now from case goods. Bulk oil is probably still the best route for dealers that primarily use one grade of oil however it no longer meets my needs since I have limited space and I am unable to have multiple bulk tanks. I recently investigated "bag-in-box" rack systems. For those of you who are unfamiliar, "bag-in-box" is 6 gallons of oil in a cardboard box with a plastic bag "bladder" that has a spigot. The 6 gallon boxes are stored on a rack that has graduated pitchers under each box. Open a spigot, fill the pitcher to the desired amount, pour the pitcher into the engine. No large bulk tank, no pump, no piping, no overhead reel. The size of the 6 gallon box (24 qts) is about the same size as a regular case of oil (12 qts). I had a meeting with a sales rep from GH Berlin Windward yesterday. They offer "bag-in-box" rack systems from Kendall, Valvoline, Mobil, Chevron, Peak and Navi-guard (house brand). Are any of you using a "bag-in-box" rack system? Do you have any comments or tips?
- 10 replies
-
- Bag-in-box oil
- oil
-
(and 2 more)
Tagged with:
-
I agree with ncautoshop to limit phone or walk in estimates except for common work. I use our shop management program for all estimates (except common work). The estimate is retained as a quote for that customer, for that car, until the job is completed or I manually clear it. I have the option of giving a customer a printed estimate, emailing the estimate or sending an estimate by text all within my shop management program (BayMaster). This works well, requires no hand written folder of papers and can be recalled in seconds at any time. Another advantage is that we have the occasional person who requests estimates but never has the work completed. Since all estimates remain available they start to accumulate indicating to us that this customer is a "tire kicker" and more than likely will not follow thru with the repairs. I sometimes have customers call and request an estimate and see that I had already completed a quote for the same work the month before. Big time saver at that time since the estimate is already completed, quick review and all done.
-
You Know You're A Mechanic If --- Take the test, see if you pass
JimO replied to Gonzo's topic in AutoShopOwner Articles
Great article, thank you. -
We rarely have a slow day and realize how fortunate We are. Years ago we would usually by clean, used vehicles that had great curb appeal but were mechanical disasters so the purchase price was minimal. We would purchase these vehicles at any time of the year and we would do nothing to them until we had a slow time and then use them as fill in work. We have a large property so having a few vehicles on our lot for that purpose had no impact on us. Remember I said CLEAN used vehicles, nothing that would visually be detrimental to our appearance. Also we would concentrate on vehicles that we considered desirable so we knew we could quickly sell them when completed. It is difficult to make a profit from an oil change. Offering an oil change, car wash, vacuum interior, 61 point check, brake inspection and battery test for $34.95 is a definite loss if there are no additional sales generated. My worry with this approach is that it cheapens your work making it difficult to be compensated for those tasks or similar tasks in the future. I never went that route and feel bad that anyone should be put in a position to have to give their labor away. As time passes it seems that more and more services are eliminated due to technology. Oil changes are still required but most vehicles have long service intervals. Are we being reduced to doing an occasional oil change with other free services at a greatly reduced price and no profit?
-
Anyone using Text Messaging
JimO replied to Joe Marconi's topic in Management Software, Web Sites & Internet
Mathew Lee, I find that most of my messages are structured to drive a text response no call. I am sending a text messsage to save myself time, if I were to structure my text messages "to drive a call - not a return text." then I may as well pick up the phone and call the customer according to my timetable and availability rather than waiting for a return call from my customer. Our shop management system allows customizing of all outgoing canned text messages and we have structured them to be very inclusive of the common questions that customers would have. Our shop management system also automatically includes invoice total if desired eliminating our time to input these figures. We also text estimates with generalized description of work and a request that customer text back approval. In this case receiving a text is a good, desired response since it documents the owners approval of the work. I have the option of printing all text correspondence on the finished invoice which is date/time stamped. I do not use the text feature for every invoice, the phone or an in person review is still required in many cases and can not and should not be avoided. I think most experienced shop owners would be able to quickly discern when it would be appropriate to utilize this time saving option that is now available to us. -
Anyone using Text Messaging
JimO replied to Joe Marconi's topic in Management Software, Web Sites & Internet
I noticed in other posts not in this thread that some people commented negatively that they want to talk to customers as opposed to sending a text. There are situations that require a phone call and a text would be wrong or not appropriate. Informing someone that's their vehicle is completed or that ordered parts have arrived can easily be handled with a text message. I feel that these negative comments are from people who have no ability to efficiently send a text message. My shop management program (BayMaster) gave me the ability to send text messages over a year ago and I could not be without it. It is quick, efficient, documents quick comments and ALL of my customers love it. The majority of my customers are at work while their vehicle is being repaired and they appreciate the text message as opposed to a phone call that may interrupt their buisiness day. Since the text is sent using my shop management program it does not require accessing another program or entering phone numbers. I left click "Text message" on the customer screen to quickly send a variety of canned messages "You vehicle is completed" or "An ordered part for your vehicle has arrived" or "Please call us". Additional information such as our name, phone number and hours of operation is also included in these canned messages. We also can't ignore that the younger generation does not want to talk to anyone and would rather receive a text message. -
TPMS services....why didn't I think of this sooner
JimO replied to CAautogroup's topic in Tires and Tire Services
I agree with Dave, the NAPA sensors worked out well for us using the NAPA tool and my Snap-On Solus Edge scanner when needed. Unfortunately all NAPA stores in our area changed over to CarQuest so we needed a new supplier. One of our wholesale tire suppliers had a special that included a free Smart Sensor Pro tool with the purchase of (8) Smart Sensors. So far the tool and sensors have worked great, they are clonable and have very good coverage. I had a few questions initially and their support is very good. Another bonus - updates are free for life. The Smart Sensor Pro has an OBDII connection useful not only when replacing sensors but also for TPMS resets post rotation which is required on many vehicles. In the rare case we use an OEM sensor then we use the Solus Edge to introduce the new Sensor (if required). -
Tool to reset oil change lights
JimO replied to CAautogroup's topic in Automotive Shop Tools & Equipment
We use a Snap-On Solus Edge which so far has been successful on all applications that require a tool in order to reset. The Solus Edge also has easy to follow information for reset procedures that do not require a tool although we will usually access those reset procedures that we are unfamiliar with by using Mitchell On-Demand. Completing an oil change and not being able to reset a service indicator is a poor position to be in and the Solus Edge eliminated that problem. -
How did you become a repair shop owner?
JimO replied to Felix's topic in General Automotive Discussion
My brother signed the lease for a three bay gas station when he was 23 and I was 15. He had already graduated college with a buisiness degree and had previously sold cars at a local Chevrolet dealer. At a very early age our father taught us how to work, he taught us right from wrong and he led by example to always be honest. For the most part my brother ran the office and I worked in the shop. My father was a machinist by trade and I suppose I inherited more of his genes than my brother did since I was mechanically inclined at a young age and my brother was not. According to my father "If man made it, man can fix it" and I heard that quite often growing up. When I graduated High School I was going to get a place of my own but our father brought us together and asked us to consider a partnership. The next week I bought half of "the station" from my brother and a few years later we purchased our building and property. We have seen many changes over the years and I have to question if we would be able to achieve the early success we had if we we starting out now. Start-up costs and knowledge were minimal back then compared to what is now required. And Dad was right, being self employed requires that you wear many hats and it is difficult to do that alone, our partnership made us stronger and successful. We recently celebrated or 45th anniversary! -
One Parts portal for different vendors
JimO replied to HarrytheCarGeek's topic in Automotive Parts & Suppliers
I looked at Parts Tech after I read about it on this forum. The site seemed OK however I had some questions and decided to call them. Eric answered the phone and he apologized and quickly explained that he had a conference call and asked me to call back later. I have tried calling them over ten times since and only get a recorded message. I left a voice mail message on Friday and I am still waiting for a return call. The concept seems good but they must be short staffed or not ready for live use. I gave up, I have too much to do during the day besides trying to call an unmanned or poorly staffed business. -
Joe's analogy is correct. The Advance acquisition of CarQuest came early to my area. The change was NOT good, no benefit only detriment. The Advance DIY business model was apparent to me based on the following: 1) Increased cost and list pricing. 2) Elimination of parts required by us but not required by the DIY's. 3) Print and radio spots offering "no charge" code reading, battery tests and battery replacements which not only placed Advance as my competition but also degraded the knowledge, equipment and effort required to diagnose a modern vehicle to a mere "no charge" accommodation. Now the good news concerning Joe's last sentence about the big guys not changing. On Friday afternoon I received a call from a member of a business investment research firm who was hired by a group of investors to review Advance Auto Parts as a possible investment opportunity. This gentleman contacted me and reviewed my feelings about Advance because in the past I had posted comments about Advance on Auto Shop Owner. We need to know that our comments, praise or criticism, are being viewed by other people and some of them are Wall Street people. We never had an independent public platform that could reach so many people before. I am ashamed to say this but I never talked about business with shop owners in my immediate area no less the amount of people this forum reaches. We need to talk, we need to realize and understand that we are all facing similar problems and maybe together with careful consideration and open discussion we can make a change. Thanks again Joe for another great post.
-
My post today strays a bit from the Auto Zone code testing topic but instead addresses some comments made within this thread concerning our image and how it is portrayed to the public. Lately Ford has been running advertisements in our trade publications and on the web for FordParts.com. Ford is clearly depicting us all as a group of workers with dirty, greasy, oil soaked hands. That image is an insult to me and it should be an insult to all of us in the trade. I personally will never use FordParts.com because of this blatant disrespect from a company that should know better. I have emailed my feelings to FordParts.com and I urge everyone else to do the same.
- 27 replies
-
- Diag testing
- Free check engine light tests
-
(and 2 more)
Tagged with:
-
Heater Core Replacement for a 96 Ford E350
JimO replied to 5 Star Auto Spa's topic in Technician Corner - Discussions
For a 1998 5.4 Expedition Mitchell allows 7.0 for the core + 1.4 for evac/recharge of A/C = 8.4 hrs. Was anything else required such as hoses, coolant flush, initial review/diagnosis? Either way this is a long, tedious job that I would normally recommend go to the dealer. I happen to be busy enough to have that luxury. If I had to do the job I would go in at 9-10 hours PLUS the unknowns which I noted above. Sorry you wound up short but your tech possibly learned something during that job and you definitely did. -
Heater Core Replacement for a 96 Ford E350
JimO replied to 5 Star Auto Spa's topic in Technician Corner - Discussions
You failed to give exact info for the vehicle but when I checked Mitchell, Motor and Chilton with various engine, transmission and sub-model configurations for a 1996 Ford Econoline I fail to see any time estimates anywhere near your stated 7.3 hours. In fact they are all much less which confuses me. Is it possible that the vehicle was mis-identified on your post? -
I text customers using my shop management program, Baymaster. The program does not use my phone lines, everything is done on the Internet through BayMaster. When I complete an invoice I am able to choose "Text" and the program sends a text message that the vehicle is completed and includes total invoice, hours we are open, our phone number and "Thank you". This canned message can also be changed or customized as needed. I also send canned messages for "Job in progress", canned updates that "Ordered parts have arrived" and canned estimates for proposed work. I also send text messages when I want additional documentation of a problem such as - "Needs brake lines replaced due to rust/corrosion. Dangerous condition". All messages are printed on the final invoice. Customer's continually tell me how much they like being kept informed via the texting. It takes me 10 seconds to text a customer with needed information instead of phone calls that take much longer and all too often are forgotten or neglected due to interruptions.
- 16 replies
-
- texting
- text messaging marketing
-
(and 1 more)
Tagged with:
-
TIRE PRESSURE SENSORS, WHAT ARE PEOPLE USING?
JimO replied to sparkerauto's topic in Automotive Parts & Suppliers
I have been using NAPA Quik Sensors, very good coverage with five part numbers. We use the NAPA TPMS tool that clones the Quik sensor to the original. Very fast and I have not encountered a problem yet. Previously I used OEM sensors and introduced when needed with Snap-On scanner. This presented three problems- (1) Delays obtaining the sensor from the dealer. (2) Smaller profit margin on the OEM sensor. (3) Added time introducing new sensor (when required). On the rare occurrence that a NAPA Quik sensor does not offer a sensor for an application then I use OEM. -
Shop Management Software
JimO replied to silvasauto's topic in Management Software, Web Sites & Internet
I have been using Baymaster for the past five years and I have been very satisfied. Integration with Identifix and major parts and tire suppliers. Ability to send text message when job is completed or when parts arrive (customers love that feature). Completed invoice looks professional. Customers are able to understand the invoice. Uses CarFax to obtain VIN, make, model, sub-model and engine size just by entering the plate. Support is excellent and they are open to suggestions as to what we need and they make changes accordingly. Before getting Baymaster I looked at Mitchell and found it too difficult comparing it to Baymaster and to what I had been using. The support was nothing like Baymaster and Mitchell lacked features that I needed. I have used Mitchell for repair information for over 40 years and it has been my experience that the product itself is good but the support falls short. I have sent email message from within the Mitchell site requesting help or a concern with functionality multiple times and they have never responded. -
Shop Management Software
JimO replied to silvasauto's topic in Management Software, Web Sites & Internet
-
I appreciate this post. I have been in buisiness for 43 years and in the beginning I used aftermarket pads and rotors without problems. In the early to mid 80's we started getting noise complaints that the aftermarket blamed on our workmanship. We changed to OEM friction and all noise problems went away. Since then I would get aftermarket reps come in explaining they did have noise issues (but blamed the installer) and now they are new and improved and will not make noise. Too late, too many jobs redone for free under warranty. Aftermarket would be easier for me and possibly more profitable so I am interested in the responses. I have another issue - there are too many aftermarket brake pad choices. Very easy to order one and only one, correct OEM pad that will fit and be quiet. I am amazed at the endless choices of aftermarket pads within one manufacturer.
-
Welcome Gary! Good luck with your career change.
-
I use Baymaster shop management software for almost five years and it works great for my needs. You are correct that there were many incorrect prices blamed on computer glitches. I am bad with time but I believe it was in 2013. These "glitches" caused me to investigate all pricing and compare. Almost every price comparison resulted in the Advance pricing having a higher cost and a greatly exaggerated list price. My shop management information would indicate everything was ok because my profit margin was ok. In fact my profit margin looked better than average due to the exaggerated list price of the Advance parts. Non professionals walking into an Advance store never paid anything near the list prices that Advance was supplying me with. I feel the prices were falsely inflated to hide or conceal the increase in our cost price. I supplied endless printed price comparisons and finally gave up since no corrections were being made. I still have access to Advance pricing and purchase from them occasionally but the prices continue to have higher cost/list pricing. The interface with Carquest was the best. For my requirements no other supplier comes close to matching that but unfortunately it is gone. Back when my Advance sales rep would stop in he said that Advance would be changing over to the Carquest system but that has not happened. I have not seen my Advance sales rep in 6-12 months so if change is coming I am not aware of it. Advance uses something else or an altered version. My Napa supplier does not use the Napa interface and instead uses Nexpart which is at best ok and not even close to Carquest. I am now a Napa Car Care center and I find the benefits, training and support are all similar to Carquest so no loss in that area.
-
I was a former Technet member and did very well with Carquest. As the changeover took place I noticed our costs went up and list prices went way up in most Advance lines. It is very easy to look at tremendous profit margins from false, inflated list prices and think everything is great, don't be fooled. Belts, hoses, wipers and exhaust pricing seemed to be ok but all other lines were distorted with elevated cost and greatly exaggerated list prices. Numerous stocking Carquest lines were never changed over to Advance and sat fallow with no ability to efficiently sell since my shop management interface to Carquest evaporated after the changeover. I forwarded item by item price comparisons to my sales rep who in turn forwarded them to his superiors and nothing changed. The Advanced rep stopped coming in so one by one each stocking line was changed over to Napa. The Napa shop management interface is not as good as what I had with Carquest but the prices are back to normal. I truly miss Carquest and would be with them today if possible, what a shame. I would like to see how many concerns on Joe's list align with issues that I experienced, some of which are noted above.
-
Taking Pics of Work
JimO replied to CAautogroup's topic in Auto Repair Shop Management Help? Start Here
We will take pictures on occasion and we will sometimes show the customer the actual defect or concern but we also frown on having customers in the bay areas. We will always document findings on the work order. If the work included an oil change we will document findings on the reminder sticker as well. We text the customer when the job is completed using our shop management program and we will also include remarks in the text message which is time stamped and printed on the finished repair order. -
NYS may move to biennial inspections
JimO replied to Junior's topic in Business Talk - How's your shop doing?
Here in NJ we have a hybrid system meaning we have private inspection facilities at gas stations/repair shops and we also have Central Facilities sprinkled over the state that are operated by Parsons (from California) and monitored by NJ Motor Vehicle Services. My customers have a choice of paying me for an inspection or go to a central facility and have it done for free. Over the years New Jersey has dropped safety testing and went to a two year sticker except for commercial vehicles. Worse yet they extended the new car sticker to five years. We are only allowed to inspect a vehicle that is five years old or older. There was a recent article in the paper indicating that vehicle fatalities have gone down since the safety test was dropped indicating the state made a wise decision. The same article indicated that tickets issued by police for unsafe vehicle conditions have gone up during the same time period indicating that safety issues are being identified by the police force as opposed to the inspection stations. Politician's love to please the public and doubling the life of a passing sticker is something the public will embrace so change will happen. Statistics in NJ and other states that have made similar changes will convince politician's in your state that a change is required and everyone will love it except for us. Will there be unsafe cars on the road due to this change - we all know that safety has to be compromised by this move. I am not knocking the police but when was the last time you saw a cop lay on the ground during a traffic stop and inspect tread depths or raise a vehicle off the ground to check the front end, brakes and exhaust system? This is not their job, it should not be their job..... it was meant to be our job. -
I have used BayMaster for 4 years and I am very happy. The system can import list prices from either Motor or All Data. I can order place orders from suppliers such as CarQuest, Advance, NAPA, American Tire and transfer the cost/list and part number directly to the invoice. No phone calls, no mistakes transposing part numbers or pricing. I have a service reminder printer that interfaces with the program and a recent update allows me to send a custom or pre-canned text message that a vehicle is completed or parts have arrived or an estimate of repairs etc... The company is smaller than Mitchell and they have been very attentive to my needs or requests making changes accordingly which is a big bonus. They also offer partially printed invoices with a water mark like image of your location or logo. Very professional look to the finished work order. Previous to BayMaster I used a I used a DOS program called Repair Ware from Success Systems for over 20 years, no comparison to what I have now. I tried Mitchell when I made the change and found it harder to use than BayMaster and not as flexible for my needs.